Introduction: With the rise of the printing and packaging industry, packaging and printing technology continues to improve with new and high technology, the quality of the printed matter has also been significantly improved and the competitiveness of the products on the market has been considerably improved. Printing and packaging plastics is a highly specialized technology, so plastic films often cause a number of problems in gravure printing. Poor ink fastness is one of the most common problems. This article discusses some of the issues that affect ink strength factors when choosing a superior packaging material system for your reference:
Adhension fastness
The adhesion of the ink marking to the substrate is called Adhension fastness.
The ink adhesion fastness test is generally measured using a transparent adhesive tape (the adhesive force of the tape is over 2 N / 15 mm). After the ink has not been transferred or the area after the adhesion has been transferred to the tape, it is determined that the ink adhesion fastness corresponds to the standard the printing film.
The poor adhesion of the ink causes the composite film to transfer a large area or all of the ink during the development process, resulting in low bond strength, and the effective combined force between the different layers of the composite film cannot be generated, resulting in a low overall tensile strength of the composite film, which ultimately affects the bag after molding. Printing performance, and since the low bond strength bag is at risk of delamination during heat resistance, this may affect the use of the composite packaging bag.
1. The influence of the ink resin system
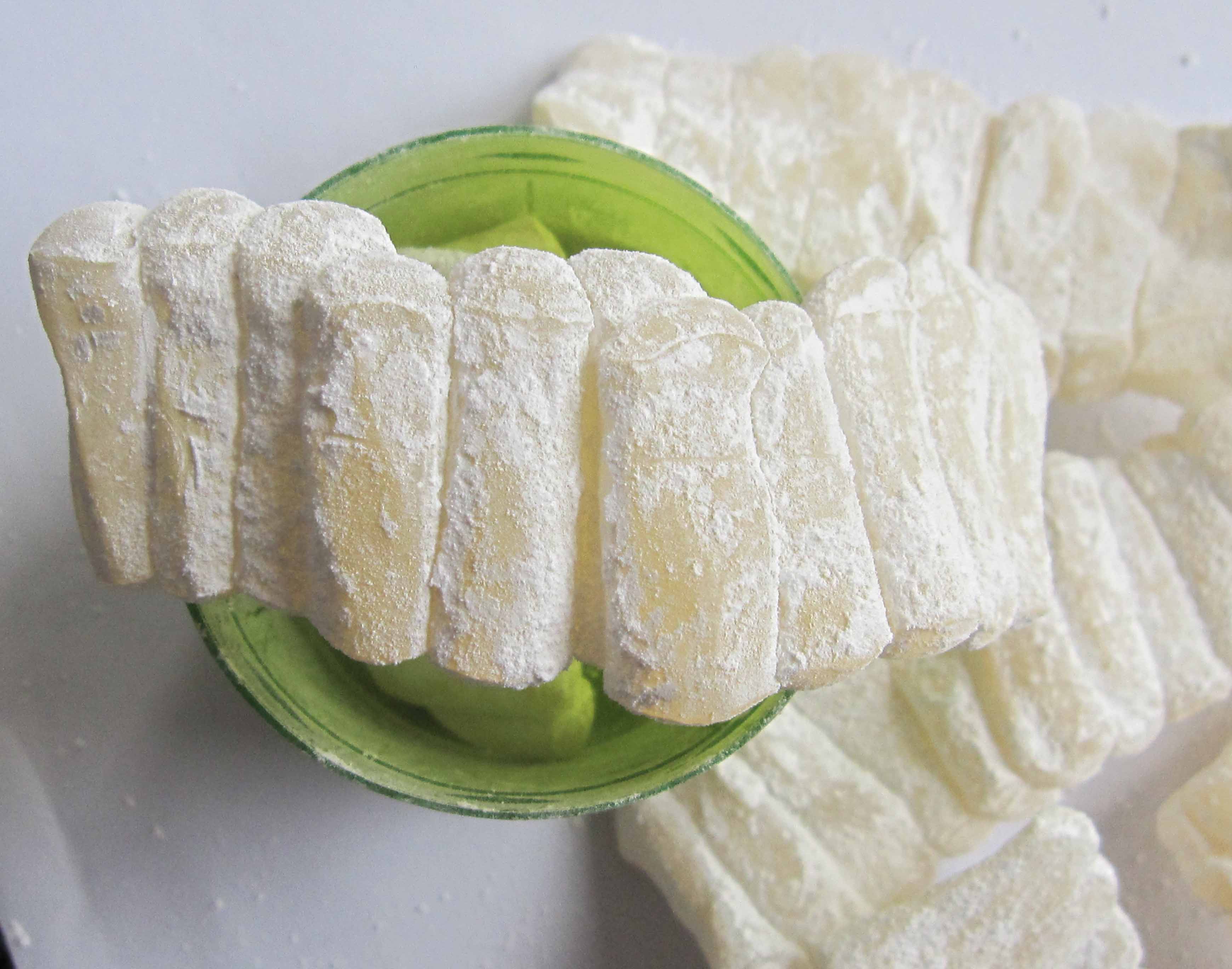
2. The influence of pigment dispersion
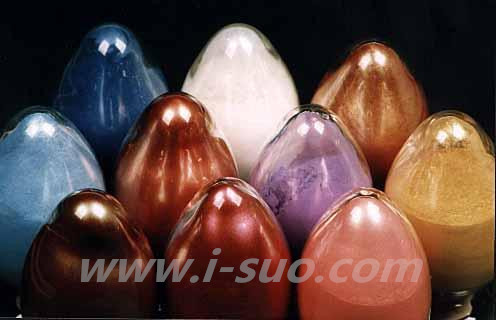
3. The influence of solvents
4. The influence of the properties of film surface
5. The influence of the moisture absorption of film