The rapid development of flexographic printing (flexo printing) technology has greatly promoted the process of ink desolvation. Flexographic printing technology uses flexible rubber letterpress or photosensitive resin plate printing, and requires the use of non-organic solvent inks that are non-corrosive to the plate material. . Traditional flexo printing cannot print high-quality images using rubber letterpress. It was not until 1973 that DuPont of the United States developed a UV-curing resin plate before printing high-precision prints. In recent years, in the packaging industry, due to the plate material (polymer photosensitive resin plate), plate making (computer direct plate making), anilox roller (laser engraved ceramic anilox roller) and closed doctor blade, printing plate cylinder sleeve method, semi-transparent The advancement of technology such as half-mirror has greatly promoted the development of flexographic printing and made it the most dynamic printing method, which has greatly promoted the rapid development of water-based flexographic inks.
1.Overseas Status
It is precisely because of the rapid development of flexo printing that the demand for flexographic inks is increasing. According to reports, flexographic inks, especially water-based flexographic inks, have become the main competitors of lithographic printing inks in newspaper printing and packaging performance printing in European and American countries. In the 1990s, flexo printing has changed from a simple and rough printing method to a printing method with the most growth and rapid development. It is estimated that by 2025, the respective proportions of flexo, four-print, and flat-print will be 25%, forming a triad of flexo, gravure and flat-printing. The market share of flexographic printing in Western Europe and the United States is growing.
2.Domestic Status
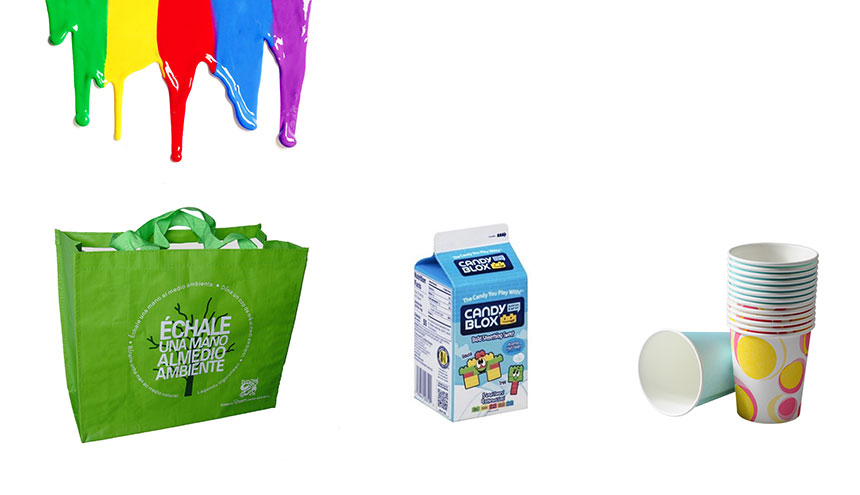
The water-based flexographic ink products that have been developed and are being developed in China mainly include:
A. Carton printing ink, but high-end packaging still uses imported ink.
B. Ink for paper cup printing, but imported ink is still used for high-end packaging.
C. After the introduction of high-quality flexographic printing inks and high-quality packaging flexographic printing machines, imported inks are now mostly used.
Because the quality of domestic water-based inks cannot meet the printing requirements! High-end printing, and imported inks are expensive, manufacturers who have introduced flexo printing machines are looking for alternatives to imported inks. Therefore, the development of high-quality water-based flexographic inks has important application value.
Now, there are primary 3 kinds of resins and 2 kinds of additives modified in the market to meet the requirements of printing ink.
Ink resins:
1. Polyamide resin
2. Acrylic resin (also including acrylic emulsion)
Besides, Epoxy resin, Polyurethane resin, and Phenolic resin, also play an critical role on the connection material of Printing ink industry.
Ink additives:
1. PE wax
2. Dispersing agent